Bar grating is an essential component in a wide range of industrial and commercial applications, offering a blend of structural strength, safety, and aesthetic appeal. The dimensions of bar grating, commonly referred to as bar grating sizes, are critical to its functionality and usability, impacting everything from load-bearing capacity to ease of installation.
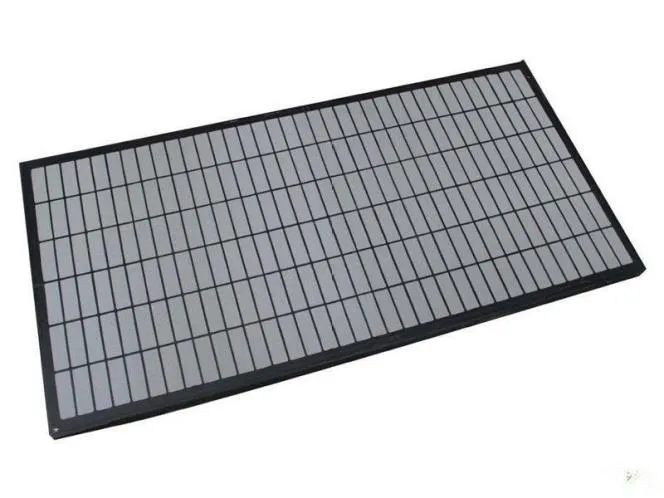
Bar grating is primarily available in two fundamental types welded and press-locked. Welded bar grating, known for its robust structure, is manufactured by welding the bearing bars and cross rods together, providing a strong load-bearing structure ideal for heavy-duty applications. Press-locked grating, on the other hand, features a locking mechanism between bearing bars and cross rods, resulting in a sleek look suitable for architectural purposes where aesthetics and safety are paramount.
Understanding the terminology used in bar grating sizing is essential for selecting the right product for any application. The primary measurements to consider are bearing bar size, spacing, and panel dimensions. Bearing bars, which run parallel to the span of the grating, constitute the main load-bearing element. Their size is typically indicated by height and thickness, which can range from 1 inch in small applications to over 3 inches for heavy industrial use, with thicknesses typically varying from 1/8 inch to 1/4 inch.
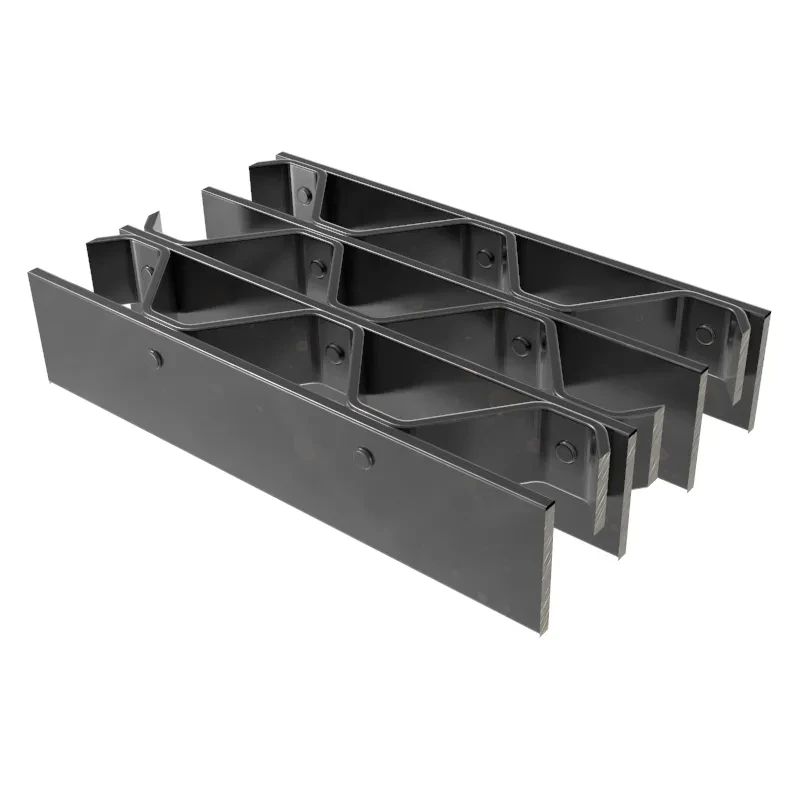
Spacing of the bearing bars and cross rods forms the second key parameter, often represented as center-to-center spacing. Common spacing sizes range from 19-w-4 (19/16 inches) to 7-w-4 (7/16 inches). This measurement influences both the load capacity and the open area of the grating—wider spacing offers more open area, which can be beneficial for drainage and ventilation, but may compromise load-bearing capacity.
Finally, the overall panel size of bar grating is determined by the application requirements. Standard panel widths are usually 2, 2.5, or 3 feet,
with lengths reaching up to 24 feet. Custom sizes are also available to match specific installation constraints, ensuring ease of fitting and alignment during assembly.
bar grating sizes
Selecting the appropriate bar grating size involves balancing functionality and regulatory compliance. Safety standards, particularly for flooring applications, demand sufficient strength to support expected loads while ensuring stability underfoot. Industry standards, like those from the American National Standards Institute (ANSI) and Occupational Safety and Health Administration (OSHA), provide guidelines on the minimum load capacities and spacing configurations.
Durability and maintenance are also influenced heavily by the size of the grating used. Thicker and more tightly spaced gratings tend to be more durable and can withstand higher loads and more frequent use, reducing the need for maintenance and replacement. Installation aspects cannot be overlooked either; a well-sized grating minimizes cutting and reshaping, simplifying the installation process and saving both time and labor costs.
Bar grating sizing is not just about selecting a component that fits — it is about enhancing the safety, functionality, and aesthetic value of the space in which it is applied. Industries ranging from manufacturing to petrochemicals, and public infrastructure such as bridges and walkways, benefit from appropriately sized bar gratings that provide reliable performance and long-term value.
In summary, selecting the ideal bar grating size is a nuanced process that must account for the specific demands of each application, balancing load-bearing requirements, compliance with safety regulations, and desired aesthetic outcomes. Making informed decisions regarding bar grating sizes is essential to maintaining operational efficiency and ensuring the safety of the constructed environment. Whether for increased durability, reduced maintenance, or aesthetic purposes, the right bar grating size can have significant implications for both performance and cost-effectiveness in any application.