Steel grating, an essential component in many industrial and commercial applications, draws attention for its robust durability and practical value. However, the cost of steel grating can significantly impact project budgets, making it crucial to understand the different factors that influence its pricing. Through an exploration grounded in experience, expertise, authoritativeness, and trustworthiness, this article dives into the nuances surrounding steel grating cost.

Navigating the landscape of steel grating begins with understanding the materials involved. Steel grating is typically made from carbon steel, stainless steel, or aluminum, each varying markedly in price. Carbon steel is the most economical option, offering substantial strength; however, it requires proper coating to prevent rusting. Stainless steel, while more expensive, provides superior resistance to corrosion and doesn't require additional protective layers. Aluminum grating is valued for its lightweight and corrosion-resistant properties but comes with a higher price tag.
Another pivotal factor in steel grating cost is the manufacturing process. Gratings can be manufactured through welding, pressure-locking, or swaging techniques. Welded steel grating is the most economical and widely used, favored for its strength and simple construction. Pressure-locked grating offers a higher degree of customization and aesthetic appeal, appealing to projects where appearance is as critical as cost. Swaged grating, primarily with aluminum, is utilized where lightweight characteristics are prioritized, often increasing the cost due to the intricate manufacturing process.
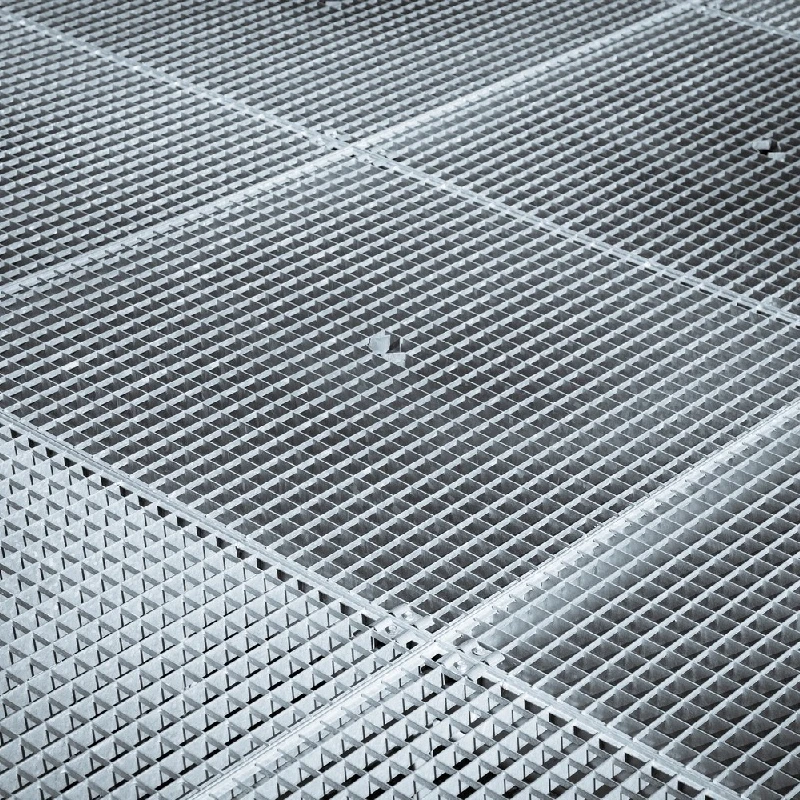
The dimensions and specifications of the grating play a crucial role in determining costs. Standard panel sizes generally offer cost benefits, whereas custom specifications, requiring bespoke manufacturing solutions, tend to escalate prices. The choice of mesh size also influences price. Larger openings require less material, reducing cost, whereas smaller mesh sizes enhance precision and load distribution, impacting the overall expense.
Understanding market dynamics is essential in managing steel grating costs. Prices of raw steel fluctuate due to factors like geopolitical tensions, international trade policies, or changes in supply and demand dynamics. Staying informed about these changes can help businesses better predict cost variations and time their purchases more strategically.
Volume purchasing power is another element affecting the cost. Buying in bulk can lead to significant savings, as manufacturers often provide discounts on large orders. This is a strategic advantage for large-scale projects, where ordering substantial quantities can offset costs significantly. However, storage costs and the risk of over-purchasing should be assessed carefully to determine whether bulk purchasing aligns with overall project goals.
steel grating cost
Installation methodologies also add layers to total grating costs. While DIY installations might seem cost-effective, professional installation guarantees correct fitting and enhances safety, ensuring durability and adherence to safety standards. In many cases, an investment in skilled labor upfront reduces long-term maintenance costs and liabilities.
Sustainability in materials is becoming increasingly vital. Higher upfront costs in selecting environmentally friendly materials can pay off, as sustainability not only supports corporate social responsibility goals but can prevent future regulatory compliance costs. Additionally, utilizing recycled materials where applicable can cater to niche markets prioritizing eco-friendliness, aligning with broader market trends towards sustainability.
Maintenance requirements, often overlooked, are integral in cost evaluations. Steel grating solutions with protective coatings and rust-resistant properties, like stainless steel, offer longer service life and reduced maintenance expenditures. By evaluating the total cost of ownership, rather than focusing solely on the initial purchase price, businesses can optimize both budget and material utility over time.
Engaging with authoritative industry manufacturers and consultants can provide guidance tailored to specific project needs. These experts bring valuable insight, identifying cost-effective solutions that do not compromise on quality. An investment in expert advice can mitigate risks associated with improper material selection and inadequate specification adherence.
In conclusion, navigating steel grating costs demands a multilayered approach, considering material choices, production methods, market conditions, and total lifecycle costs. Expert evaluations and strategic purchasing can transform what seems to be a straightforward procurement decision into a well-informed strategy that maximizes both fiscal and project-specific outcomes. Trusting experienced professionals ensures that projects not only stay on budget but also surpass quality and longevity expectations, cementing steel grating as a cornerstone of industrial and commercial infrastructure solutions.