Offshore pipelines are crucial in the transportation of oil and natural gas from offshore oil fields to onshore facilities. This intricate system requires robust constructions that can withstand harsh marine environments. A pivotal element in the construction of these pipelines is the use of counterweight solutions, particularly the innovative application of welded wire mesh as counterweights.
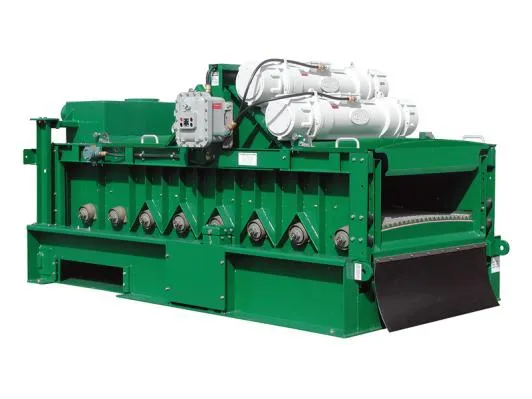
Welded wire mesh counterweights serve as a critical component in stabilizing offshore pipelines. These counterweights are engineered to prevent buoyancy, a challenge posed by submerged pipelines that can lead to alignment issues and potential ruptures. The uniqueness of welded wire mesh lies in its exceptional durability and versatility. Unlike traditional concrete counterweights, welded wire mesh provides a flexible yet strong framework that can be customized to specific pressures and movements linked with underwater currents and tidal forces.
Experience plays a significant role in understanding the deployment of welded wire mesh as counterweights. Real-world application insights reveal that its lightweight nature simplifies the installation process, minimizing the labor and equipment costs typically associated with counterweight installations. Moreover, the adaptability of welded wire mesh ensures compatibility with various pipeline diameters and materials, making it a preferred choice among engineers and construction experts.
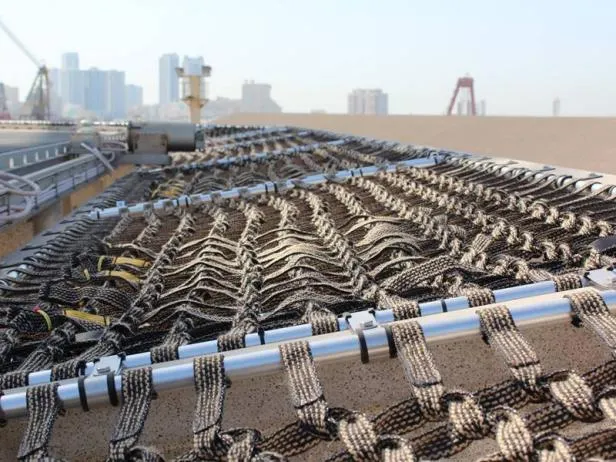
Expertise in marine engineering underscores the superiority of using welded wire mesh counterweights. Marine environments are notorious for their corrosive elements, and traditional counterweight materials may deteriorate over time. However, through expert knowledge and innovative design, welded wire mesh is crafted using high-grade stainless steel or galvanized steel, offering unparalleled resistance to corrosion. This quality ensures the longevity of the pipeline infrastructure, drastically reducing maintenance costs and enhancing the operational lifespan of the pipeline networks.
offshore pipeline counterweight welded wire mesh
Authoritativeness is further emphasized by the adoption of welded wire mesh by leading global engineering firms. These firms recognize that traditional methods are gradually becoming obsolete due to their inefficiency in rapidly changing marine conditions. Through rigorous testing and compliance with international standards, welded wire mesh counterweights have proven their efficacy in various offshore environments around the world. Their adoption is supported by comprehensive industry certifications that affirm their performance and reliability.
Trustworthiness is built through transparent processes and verifiable results when using welded wire mesh counterweights. Case studies have demonstrated successful deployment in projects where environmental considerations were paramount. The eco-friendly manufacturing process of welded wire mesh, coupled with its recyclability, aligns with sustainable construction practices. These characteristics not only protect marine biodiversity during installation but also ensure that the removal or replacement of counterweights imposes minimal environmental impact.
For engineers seeking to integrate welded wire mesh counterweights into their projects, collaboration with experienced suppliers and manufacturers specializing in marine engineering is crucial. These partnerships enable a seamless transfer of knowledge and technology, ensuring that the application of counterweights meets specific project demands while maintaining compliance with safety and environmental standards.
In summary,
offshore pipeline stability is increasingly reliant on innovative counterweight solutions like welded wire mesh. Its design adaptability, enhanced durability, and environmental benefits distinguish it from conventional materials. With an understanding driven by experience and expertise, and backed by authoritative endorsements and trustworthy practices, welded wire mesh stands out as the future of counterweight solutions in offshore pipeline construction.