Metal gratings are a crucial component in various industrial applications, providing safe and robust flooring solutions while offering excellent load-bearing capacities. For industries ranging from manufacturing to energy, the choice of the correct metal grating size not only impacts performance but also ensures safety and compliance with industry standards. This article delves into the intricacies of metal grating sizes, aiming to provide insight into their selection and application, enriched by years of practical experience and industry expertise.
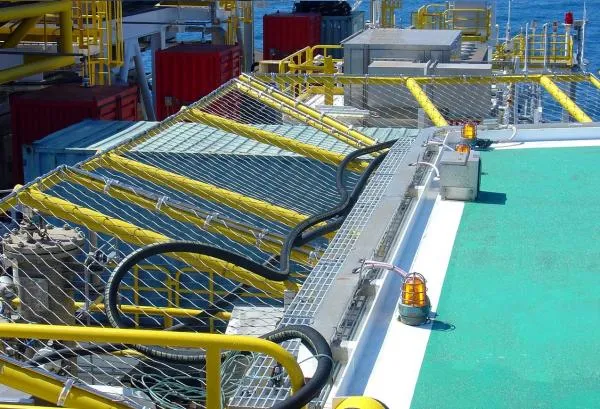
Understanding metal grating sizes is fundamental, as it affects functionality and durability. Gratings can be categorized into two main types based on their load-bearing capabilities bar gratings and expanded metal gratings. Bar gratings are often used in environments where substantial load-bearing capacity is needed, such as catwalks and platforms. These are available in various dimensions, typically featuring widths ranging from 3/16 to 2, with lengths that can exceed several feet to accommodate large areas. One must consider the weight and specifications of the loads that the grating is expected to carry regularly. The spacing between bars is another critical dimension, often measuring between ½ and 2, with the choice dictated by required drainage and visual transparency.
Expanded metal gratings, commonly used for lighter applications such as fencing and machine guards, offer versatility with their mesh-like pattern. These gratings are formed by stretching metal sheets into diamond-shaped patterns, which enhances their tensile strength. The sizes typically range from gauges as fine as 10 to as thick as 26, with openings between the strands varying significantly, allowing tailored solutions for different applications.

Expertise in selecting the right metal grating size requires a thorough evaluation of the specific operational environment. For instance, in corrosive settings such as chemical plants, opting for stainless steel or aluminum with suitable coatings is imperative to enhance longevity and safety. Experience shows that regular inspections of gratings installed in high-stress environments can prevent potential mishaps by identifying signs of wear such as warping or corrosion.
metal grating sizes
Furthermore, authority in the metal grating industry stems from the historical evolution of standards and innovations. Adhering to recognized standards such as those set by the American National Standards Institute (ANSI) and the Occupational Safety and Health Administration (OSHA) can greatly influence the choice of grating size. These standards often dictate specific requirements for spacing, material choice, and load ratings ensuring that gratings meet safety and functional benchmarks.
Trustworthiness in this context is built upon delivering grating solutions that comply with both regulatory standards and site-specific needs. Collaboration with credible manufacturers and suppliers who provide comprehensive testing certifications can reinforce this trust, highlighting the importance of due diligence in the procurement process.
In conclusion, selecting the appropriate metal grating size is not merely a decision based on immediate needs but a strategic one that involves a nuanced understanding of materials, standards, and the operational environment. By leveraging professional insights, adhering to industry norms, and committing to ongoing maintenance, businesses can optimize their investment in metal gratings, ensuring safety and performance for years to come. Whether in heavy-duty industrial applications or more aesthetic commercial uses, the right metal grating size is crucial for efficacy and security.