Shale shaker screens are crucial components in the oil and gas drilling industry, serving as the first line of defense for the drilling fluid system. These screens are primarily used to separate solid particles from drilling fluid, ensuring the consistency and effectiveness of the operation. Companies constantly seek innovative solutions to maximize efficiency, and selecting the right shale shaker screen mesh is fundamental to achieving optimal performance. This article delves into the intricacies of shale shaker screen mesh, emphasizing real experience, expertise, authoritativeness, and trustworthiness.
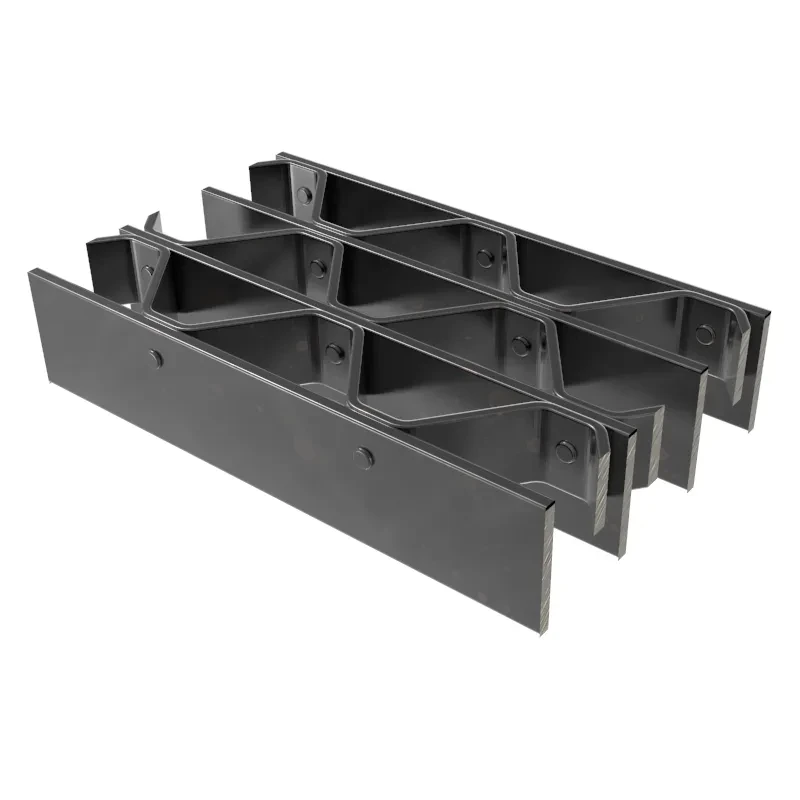
Understanding the nuances of shale shaker screen mesh begins with acknowledging its structural composition and functionality. Shale shaker screen mesh is composed of multiple layers of wire cloth with varying mesh sizes, strategically designed to optimize separation efficiency. The mesh acts as a sieve, allowing the desirable fluid to pass through while retaining unwanted solids. Experienced professionals understand that selecting the appropriate mesh size and type is critical, as it directly impacts the rate of fluid throughput and the removal efficiency of solid particles.
The expertise required for selecting the right shale shaker screen mesh involves a deep understanding of drilling conditions and screen performance metrics. For instance, the choice of mesh size depends on the particle size distribution of the drilling cuttings and the viscosity of the drilling fluid. Professionals leverage their expertise to recommend mesh configurations that minimize blinding and maximize cuttings discard. An expertly chosen screen mesh can enhance wellbore stability and reduce non-productive time, a metric crucial to the financial optimization of drilling operations.

Authoritativeness in the shale shaker screen mesh market arises from innovation and adherence to industry standards. Leading companies invest heavily in research and development to produce screens with improved durability, resistance to wear, and better separation efficiency. Advanced screen tensioning techniques, for example, prevent premature wear and tear, thereby extending the screen’s operational life. Additionally, authoritative manufacturers comply with API RP 13C standards, providing guidance on the labeling, testing, and designation of shaker screen specifications. Compliance with these standards assures end-users of the screen's effectiveness and compatibility with their shaker systems.
Trustworthiness is paramount in the screen mesh selection process. Drilling operations are high-stakes and costly; hence, reliability of equipment is non-negotiable. Trustworthy manufacturers not only provide high-quality products but also offer comprehensive support to drilling operations. This support includes pre-installation consultancy, on-site training, and after-sales service to address any operational challenges that arise. Transparency in the manufacturing process and supply chain increases customer trust, as buyers are assured of receiving the products as promised.
shale shaker screen mesh
Real-world application of shale shaker screen mesh further accentuates the blend of experience, expertise, authoritativeness, and trustworthiness. Field tests and operational feedback are valuable to mesh manufacturers, guiding the continuous improvement of screen designs. For instance, an operator's feedback on increased fluid loss might prompt a manufacturer to enhance mesh permeability without compromising solid separation efficiency. This iterative feedback loop fortifies the product's reliability and performance, cementing the manufacturer’s reputation as both an industry expert and a trusted partner.
Innovative breakthroughs in shale shaker screen technology have seen the introduction of three-dimensional screen designs, which significantly improve fluid handling capacity and solid separation efficiency compared to traditional two-dimensional screens. Such technological advancements are backed by exhaustive laboratory testing and field pilot programs, enhancing the authoritative stance of the innovator.
The investment in shale shaker screen mesh should not be underestimated. Choosing the wrong mesh can result in suboptimal drilling conditions, leading to expensive downtime and potentially compromised well integrity. Thus, aligning with reputable manufacturers who demonstrate proven expertise and deep industry knowledge is non-negotiable for drilling operators aiming to maximize their operational efficiency.
In conclusion, the value of shale shaker screen mesh goes beyond mere separation of solids and fluids. It embodies a fusion of technological innovation, operational expertise, and stringent adherence to quality standards. Companies that master these elements position themselves as leaders in the drilling industry, providing products that meet and exceed the evolving demands of modern drilling operations. By prioritizing experience, expertise, authoritativeness, and trustworthiness, stakeholders can ensure that their shale shaker screen mesh choices align with their strategic goals, securing a competitive edge in the dynamic energy sector.