Galvanized grating has become a mainstay in diverse applications, ranging from industrial flooring to safety platforms. The popularity of galvanized grating lies in its durability, resistance to corrosion, and ability to bear substantial weight. Understanding the different sizes of galvanized grating is crucial for engineers, architects, and construction managers when tailoring solutions for specific projects. This detailed guide explores the various sizes available and their optimal applications, ensuring project success with the right fit.
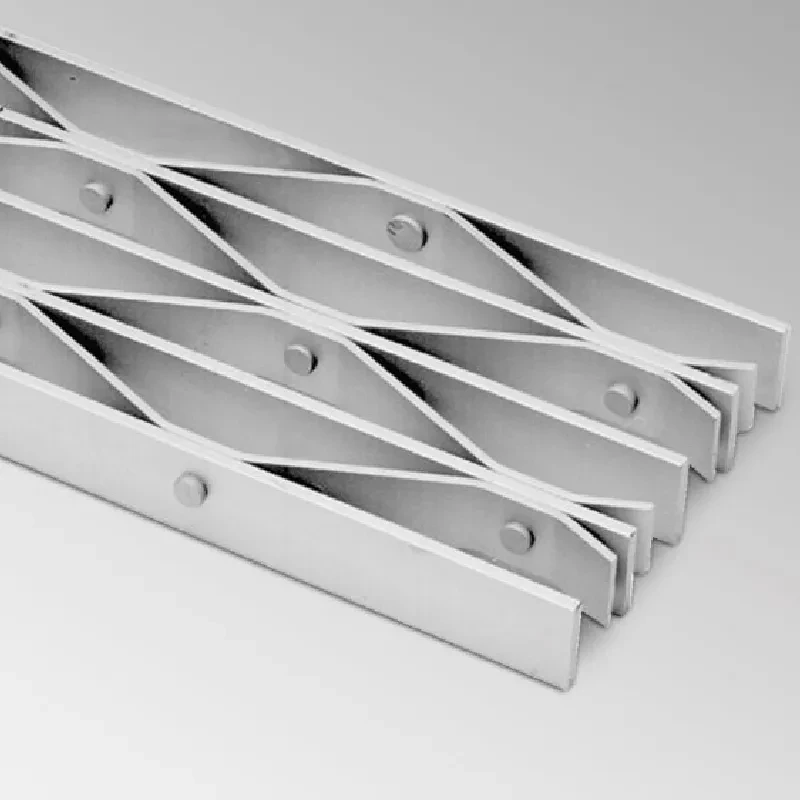
The size of galvanized grating is primarily determined by the dimensions of its bearing bars and the spacing between them. Commonly available sizes feature bearing bars with depths ranging from 20mm to 70mm and thicknesses between 3mm to 5mm. These parameters are critical for determining the load-bearing capacity of the grating. The spacing of the bars, often at 30mm to 100mm intervals, further influences the strength and design aesthetics of the grating.
For projects where weight-bearing capabilities are of utmost importance, such as in industrial environments or heavy-duty platforms, grating with thicker and deeper bearing bars is recommended. For instance, a grating with 70mm deep and 5mm thick bars provides robust support, accommodating significant weight without compromising structural stability. This size is ideal for areas with heavy foot traffic or where additional equipment is frequently moved.
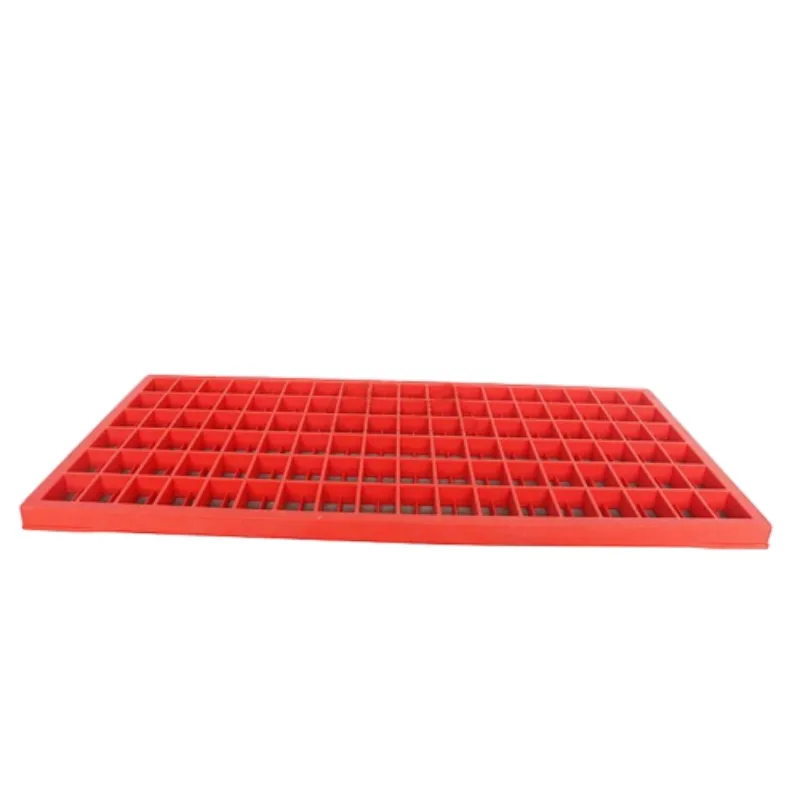
Conversely, for applications like pedestrian walkways or mezzanine flooring where aesthetic considerations might take precedence over load capacity, a grating with shallower bearing bars—about 20mm deep and 3mm thick—could be more suitable. This size offers a lighter structure while still providing enough strength to safely support pedestrians and light equipment.
galvanized grating sizes
When considering spacing, tighter patterns (e.g., 30mm spacing) not only enhance the grating's load capacity but also contribute to a safer environment by reducing the risk of accidental falls through the grating and limiting debris penetration. This makes them preferable for safety-conscious applications in public areas or over open water bodies. Wider spacing, while economically advantageous, is best reserved for less demanding environments where maximum load and safety are not primary concerns.
Another considerate factor is the type of galvanization.
Hot-dip galvanization is revered for its thorough coating, ensuring longevity even in harsh environments. It's essential to ensure that the galvanization process meets standards such as ASTM A123, ensuring robust resistance against corrosion and overall product reliability.
Engagement with a reputable vendor or manufacturer is imperative for sourcing the most suitable galvanized grating sizes. Their expertise can guide you not only through the size specifications but also materials and installation processes, fortifying the trust and durability of your project.
Ultimately, choosing the right size of galvanized grating hinges on a balance between structural demands, aesthetic considerations, and safety requirements. Properly sized and correctly installed galvanized gratings can significantly enhance the longevity and functionality of infrastructure, proving an invaluable asset to any project. Investing in high-quality grating that adheres to industry standards will ensure that your project remains durable, safe, and efficient, reflecting not only professional expertise but also authority and trust in execution.