Understanding the intricacies of metal grating prices involves a deep dive into the manufacturing processes, material selection, market trends, and industry applications. This exploration highlights the variance in pricing and underscores the value of tailored solutions.
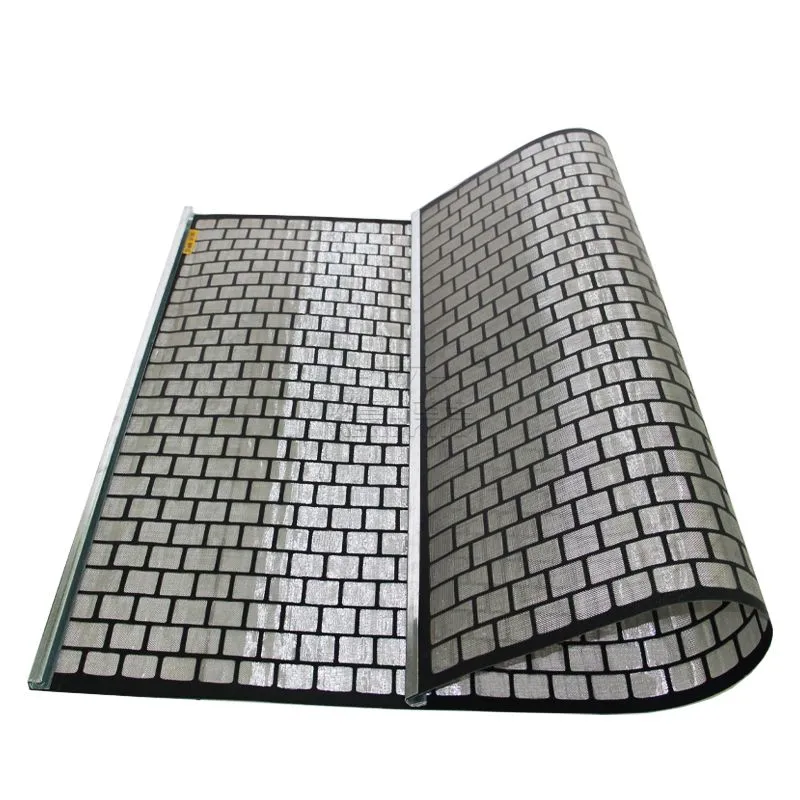
Metal grating, critical in industrial, commercial, and architectural applications, is mainly comprised of carbon steel, stainless steel, and aluminum. Each material offers distinct benefits that influence cost. For instance, carbon steel grating is often chosen for its strength and affordability, making it ideal for heavy-load environments such as industrial flooring. Stainless steel grating, on the other hand, offers superior corrosion resistance and aesthetic appeal, suitable for hygienic areas or high-visibility installations, albeit at a higher price point. Aluminum grating is prized for its lightweight and corrosion resistance, perfect for areas where weight saving is critical.
The manufacturing technique further affects cost considerations. Welded grating, known for its robust construction, is forged by fusing crossbars to load bars. This method ensures durability and is typically more cost-effective for large-scale production. Press-locked grating, meanwhile, provides a cleaner appearance by mechanically locking bars together, making it more labor-intensive and costly but aesthetically pleasing. Additionally, expanded metal grating offers a cost-effective alternative by stretching metal sheets, creating a pattern that offers traction and drainage without welding.

Market dynamics play a pivotal role in metal grating pricing. Fluctuations in raw material costs, driven by global steel and aluminum markets, directly impact the production costs. Geopolitical factors, trade policies, and environmental regulations can also alter supply chains, influencing pricing structures. Understanding these market influencers is crucial for buyers aiming to time their purchases strategically.
metal grating price
The diversity of applications for metal grating translates into variable demands. Industrial facilities often require high-load capacity grating, favoring carbon steel for its strength-to-cost ratio. Marine and chemical environments, however, may prioritize stainless steel or aluminum for their corrosion resistance despite the higher cost. Therefore, suppliers offer bespoke solutions, tailoring products to meet specific load requirements and environmental challenges, which can also influence pricing.
Expert insights suggest that potential buyers conduct thorough needs assessments before purchase. Evaluating the intended use, environmental conditions, and load requirements can guide material selection and help balance budget constraints against performance requirements. Engaging with reputable suppliers who offer transparent pricing and customization services ensures the optimal product is chosen without hidden costs.
Trust in supplier relationships is paramount, as working with established providers guarantees quality assurance and compliance with industry standards. Suppliers accredited with ISO certifications and other relevant quality marks provide confidence in the product's longevity and performance, justifying the investment cost.
In conclusion, understanding metal grating pricing involves a comprehensive analysis of materials, manufacturing processes, market trends, and application demands. By prioritizing expertise and authoritative insights, buyers can make informed decisions aligned with their specific needs, securing reliable and long-lasting grating solutions.