Helideck perimeter nets play a crucial role in the safety and functionality of offshore helipads, particularly on oil rigs, ships, and other marine vessels. These structures are not just safety nets but an essential component designed to enhance operational efficiency, ensure the safety of crew and passengers, and align with global aviation safety standards.
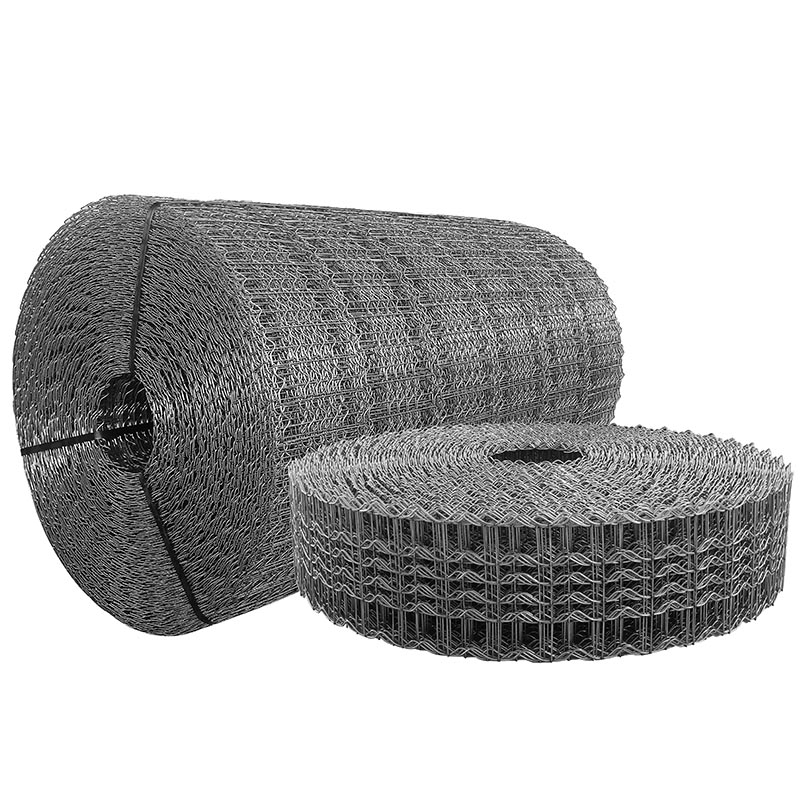
Perimeter nets are meticulously engineered to absorb the impact of helicopters during take-off and landing maneuvers. With varying helicopter sizes and weights challenging structural integrity, perimeter nets are crafted using high-tensile fibers, primarily nylon or polypropylene, providing an uncompromising balance of strength and flexibility. Their design facilitates a significant reduction in dynamic forces exerted during accidental skids or unintentional touchdowns, thus minimizing damage to the helicopter and the helideck structure.
Safety remains paramount in the helideck design process, and perimeter nets are imbued with advanced safety features to mitigate risks. Their grid pattern is methodically designed to catch any crew members or equipment inadvertently misstepping beyond the deck's edge. This not only protects lives but also secures essential tools and gear from falling into the sea, potentially preventing costly retrieval operations.
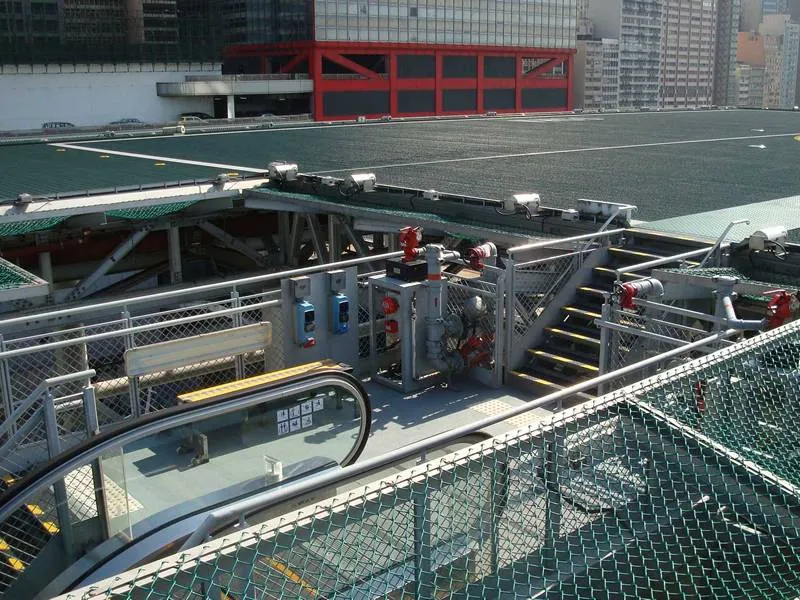
A principal element of perimeter net deployment is its compliance with international standards such as those put forth by the International Civil Aviation Organization (ICAO) and the UK's Civil Aviation Authority (CAA). These regulations stipulate specific material strength, durability, and maintenance checks to ensure the nets remain functional under harsh marine conditions. Periodic inspections and maintenance of these nets are not merely routine but a regulation-ensured practice for maintaining optimal safety conditions. The responsibility of ensuring that these nets meet and exceed regulatory requirements rests with both the manufacturers and the facility operators.
Furthermore, helideck perimeter nets are designed to withstand the abrasive marine environment, where exposure to salty air, strong winds, and UV radiation can expedite wear and tear. Manufacturers often use UV-stabilized materials to ensure longevity, reducing the frequency of replacements and thus providing cost-effective safety solutions over extended periods.
helideck perimeter net
In terms of experience,
operators note that the presence of robust perimeter nets provides peace of mind. Crews operating on and around helidecks have consistently reported increased confidence when operating within environments safeguarded by high-quality perimeter nets. This security fosters an efficient working atmosphere and reduces stress during high-traffic times, which are common during shift changeovers and crucial supply deliveries.
From an expertise perspective, industry professionals advocate for regular training in the inspection and maintenance of helideck perimeter nets. Equipped with knowledge about their functionality and service schedules, maintenance teams can preemptively address potential issues, circumventing accidents before they happen. This proactive approach heightens the perimeter nets' efficacy, reinforcing their reliability as a safety feature.
Authoritative industry voices, including those from the Offshore Petroleum Industry Training Organization (OPITO), emphasize integration of advanced materials and designs that adapt to evolving safety challenges. Newer materials and construction techniques are continuously being developed to enhance perimeter net performance, greatly influencing the design and choice of netting solutions for different helideck environments.
Trust in the reliability of helideck perimeter nets is not solely established through regulatory compliance and operator training. It is also fostered by rigorous third-party certifications and endorsements by established maritime and aviation safety bodies, which guide the net's usage in varied offshore contexts. These endorsements are pivotal for stakeholders when selecting perimeter net solutions, assuring them of the products' reliability and efficacy.
Ultimately, the strategic implementation of helideck perimeter nets exemplifies a commitment to safety and efficiency. As a product category, these nets evolve alongside technology advancements, regulatory changes, and user feedback. The collective experience and expertise leveraged in conjunction with authoritative guidance ensure that helideck perimeter nets continue to be a trusted staple in the critical operations of offshore aviation facilities.