Bar grating span is a crucial factor in the design and application of industrial flooring solutions. As an experienced industry expert, I can affirm that understanding the intricacies of grating span can significantly impact the functionality and safety of these installations. Bar grating is widely used in various sectors, from petrochemical facilities to architectural installations, due to its durability and strength. In this discussion, we will delve into the importance of bar grating span, backed by real-world expertise and authoritative insights.
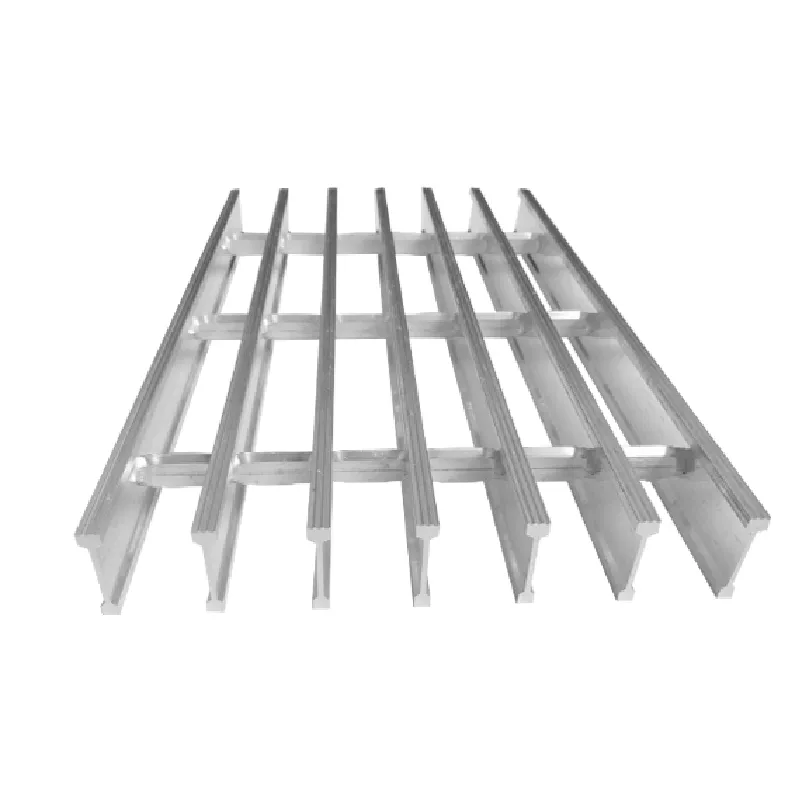
The term span in the context of bar grating refers to the distance between two supporting points on which the grating rests. Correctly determining the span is essential because it influences load-bearing capacity and structural integrity. A miscalculation or oversight in span assessment could lead to catastrophic failures in industrial settings, where safety and reliability are paramount.
In my two decades of working with different types of bar gratings — including welded, press-locked, and swaged — I have observed certain best practices that ensure optimal performance. The first step is understanding the load requirements.
Every bar grating must be designed to handle specific loads, which are either concentrated or distributed. For industrial applications, consider factors such as foot traffic frequency, equipment weight, and potential impact loads.
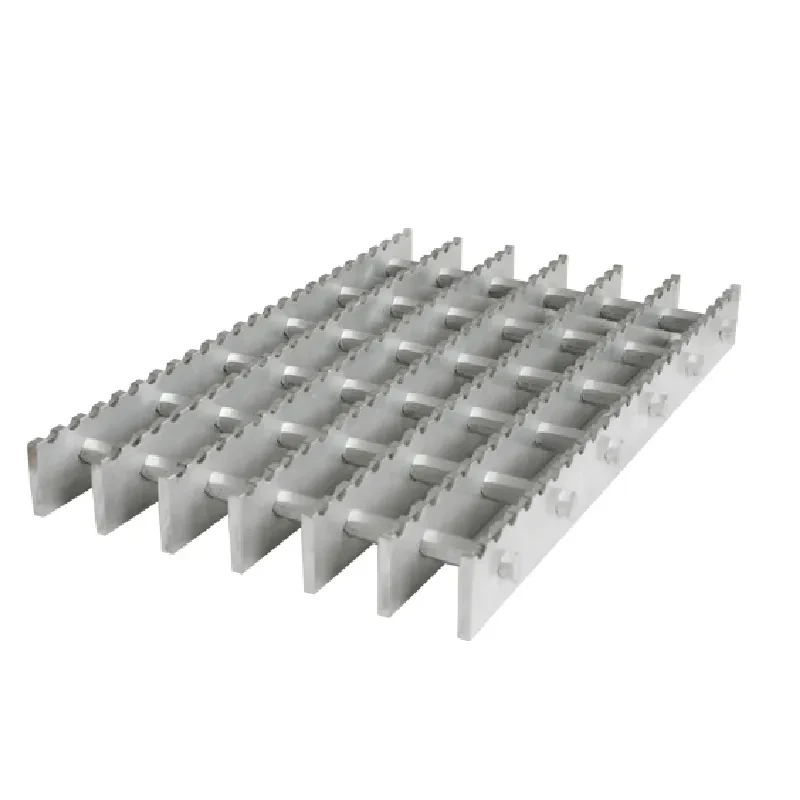
Bar grating spans are typically calculated using standardized engineering tables and formulas that incorporate load ratings and deflection criteria. These tables, often provided by manufacturers, help in selecting the correct grating size and type based on the anticipated span. When it comes to expertise, adhering to specified deflection limits—commonly set at 1/240th of the span—ensures that the grating doesn't sag under normal conditions. It is advisable to involve structural engineers in environments with complex loading conditions to validate these calculations and make necessary adjustments.
The expertise in using bar gratings lies in selecting materials optimized for the environment they will be in. For instance, stainless steel gratings offer corrosion resistance crucial for maritime or chemical exposure, whereas aluminum is perfect for installations requiring lightweight structures without compromising strength.
bar grating span
From an authority and trustworthiness perspective, choosing a reputable manufacturer is non-negotiable. Experienced manufacturers not only provide reliable products but also comprehensive guidance on span calculations and grating selection. Certifications like ISO standards are good markers of product reliability and manufacturer credibility.
I recall a client in the automotive industry who faced challenges with the existing bar grating installations in their assembly line. Improper span and load calculations led to frequent maintenance issues. After conducting a thorough analysis and collaborating with their engineering team, we redesigned the layout using a manufacturer known for high-quality galvanized steel gratings. This adjustment not only improved employee safety but also increased operational efficiency by reducing downtime.
To further ensure trustworthiness, regular inspections and maintenance checks must be adopted as part of the operational regime. This practice helps in identifying potential issues early, ensuring that the grating continues to meet its load requirements over time.
In conclusion, bar grating span is a critical element that influences the safety and efficacy of industrial flooring solutions. Leveraging expertise, selecting the correct materials, and relying on authoritative resources are fundamental to achieving a reliable installation. As industries continue to evolve, staying informed with the latest advancements and maintaining collaborations with industry experts will ensure that your bar grating applications remain at the forefront of safety and functionality.