Understanding the nuances of serrated grating weight is essential for professionals in construction and industrial applications. Serrated gratings provide a non-slip surface which enhances safety, making them a popular choice in various infrastructure projects. However, the effective use of serrated gratings hinges on a clear understanding of their weight, influencing both structural integrity and transportation costs.
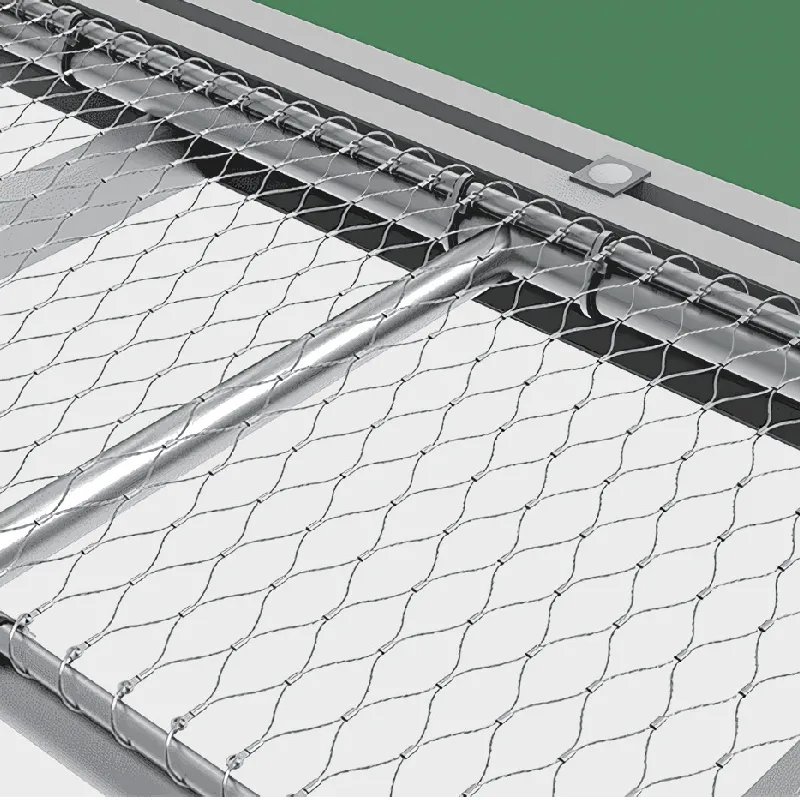
Serrated grating weight is critical for ensuring stability and safety in high-traffic areas. These gratings are typically made from steel or aluminum, materials known for their strength and durability. The choice between aluminum and steel affects the weight significantly. Steel serrated gratings are heavier, providing robust support in heavy-duty applications such as walkways, platforms, and stair treads in industrial facilities. Conversely, aluminum gratings are lighter, making them suitable for environments where ease of handling and corrosion resistance are priorities, such as marine or chemical settings.
Notably, the weight of the serrated grating is not simply a function of the material alone. The design, including the size of the load bars and spacing, plays a crucial role. For instance, gratings with thicker load bars can handle heavier loads but will consequently weigh more. Similarly, closer spacing increases the weight but provides better load distribution and enhanced safety features.
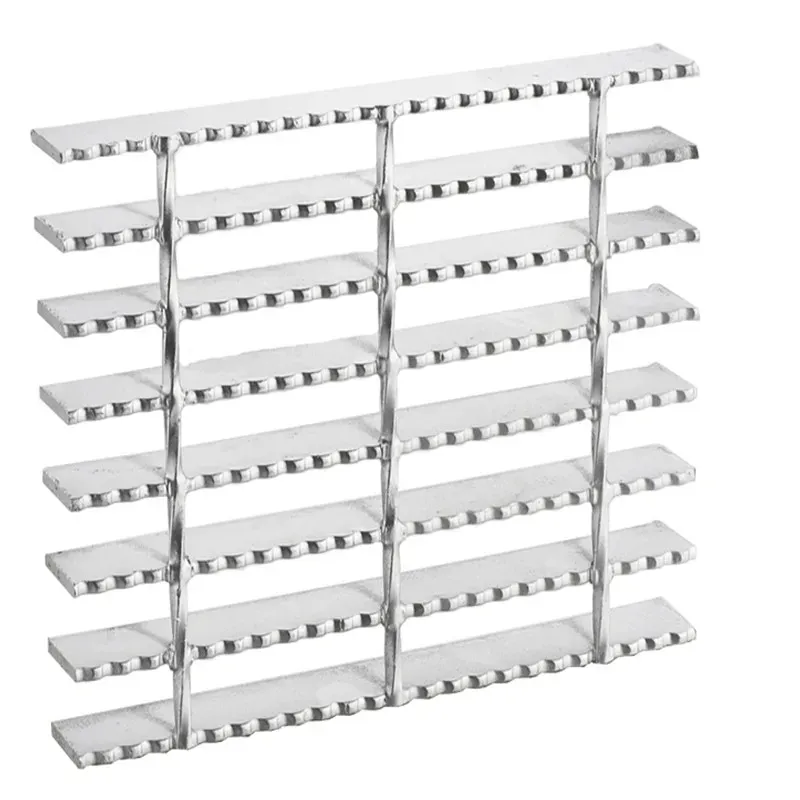
Professionals favoring experience in the field understand that the weight of serrated gratings carries implications beyond structural support. During installation, heavier gratings may require specialized equipment and additional manpower, affecting project timelines and overall costs. Furthermore, the transportation of heavy gratings necessitates strategic logistics planning to optimize shipping costs and reduce environmental impact.
serrated grating weight
For those prioritizing expertise and authoritativeness, it's essential to consult manufacturers’ specifications and industry standards when selecting serrated gratings. Leading manufacturers provide detailed weight charts and load-bearing capacities for their products, allowing engineers and architects to make informed decisions. Adhering to standards such as the ANSI/NAAMM MBG 531 for metal bar gratings ensures compliance with best practices and enhances the reliability and safety of the installations.
Trustworthiness in the selection process can be greatly enhanced by relying on third-party testing and certification. Products that undergo rigorous testing by independent bodies assure conformity to safety and quality standards, mitigating risks associated with structural failures. Additionally, engaging with manufacturers who have a proven track record of reliability and transparency in their specifications fosters greater trust.
Innovations in the materials and manufacturing processes for serrated gratings are progressing, with the introduction of composite materials offering alternative solutions. These composites provide the advantages of both steel and aluminum in terms of strength and lightweight properties, although their usage depends on specific application requirements and budget constraints.
In conclusion, the importance of understanding serrated grating weight cannot be overstated as it impacts safety, cost, and logistical considerations in the construction sector. By leveraging expert knowledge, industry standards, and trust in credible certifications, professionals can make well-informed decisions that align with project specifications and client objectives. The ultimate goal is to ensure that these gratings serve their intended function efficiently while maintaining the highest standards of safety and structural integrity.