Understanding the Cost Dynamics of Galvanized Grating
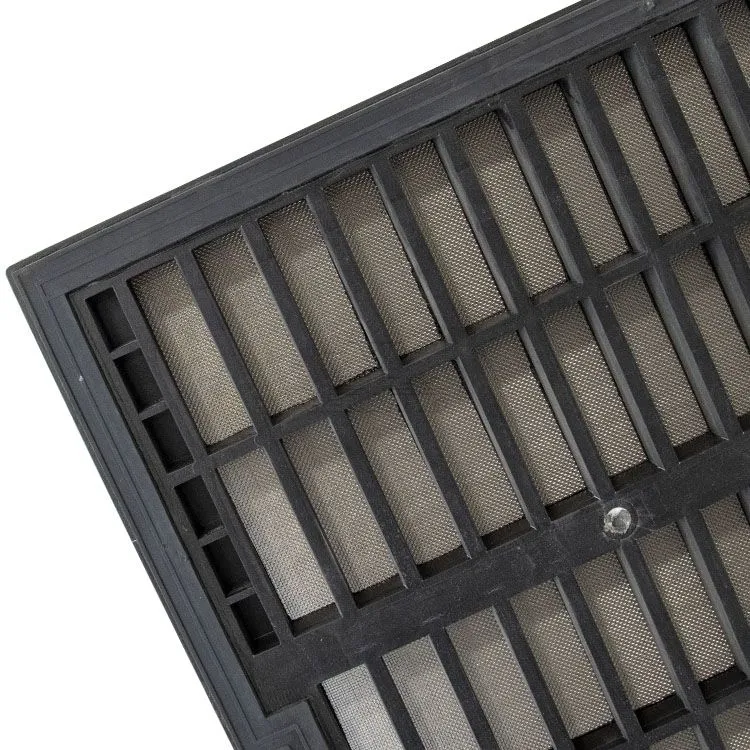
When considering construction materials that offer both durability and cost-effectiveness, galvanized grating often tops the list. Its use spans various industries, from industrial settings to residential applications, due in large part to its impressive strength and corrosion-resistant properties. However, understanding the cost implications can be crucial for budgeting and project planning. This piece delves into the factors influencing galvanized grating costs and provides insights to help navigate buying decisions effectively.
Galvanized Grating An Overview
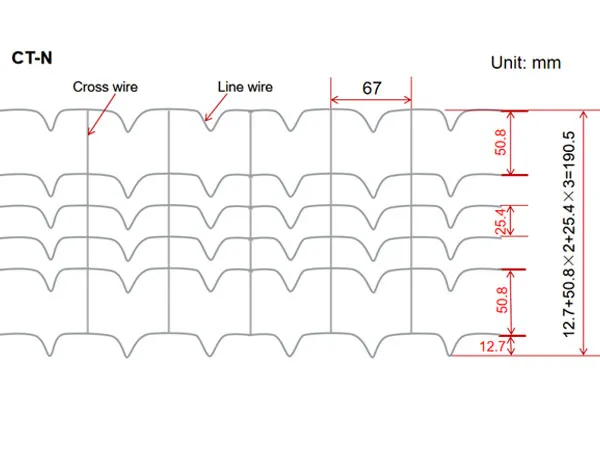
Galvanized grating, typically made from steel or iron, undergoes a galvanization process where it is coated with a layer of zinc. This process not only enhances the material’s resistance to corrosion but also extends its lifespan, making it a preferred choice for projects exposed to harsh environmental conditions. Its applications vary from flooring in industrial facilities to walkways, platforms, and drainage covers, demonstrating its versatility and wide acceptance.
Factors Influencing Galvanized Grating Costs
1. Material Quality and Type
The quality of the steel used in the grating can significantly influence the cost. Higher quality steel, offering enhanced strength and durability, is more expensive but may offer better long-term value. Additionally, the type of grating—whether it's plain, serrated, or I-bar—also affects pricing. Serrated grating tends to cost more due to its slip-resistant features, which are ideal for environments requiring enhanced safety.
2. Size and Dimensions
Cost is directly proportional to the size and dimensions of the grating. Larger projects will inherently require more material, leading to higher costs. Custom sizes or shapes can also add to the expense due to the additional manufacturing processes needed.
3. Galvanization Process
The type of galvanization—be it electro-galvanized or hot-dip—plays a role in cost. Hot-dip galvanizing typically incurs higher costs due to the extensive coating process, which offers more protection and thicker layers of zinc. The decision between the two methods depends on the specific needs of the project regarding durability and exposure to elements.
galvanized grating cost
4. Supplier and Economic Factors
Supplier pricing strategies greatly impact galvanized grating costs. Established suppliers with a reputation for quality can charge premium prices. Similarly, fluctuations in material costs, driven by global steel prices or economic conditions, could lead to price variations. It's vital to monitor these market changes and potentially lock in prices through strategic purchasing agreements.
5. Transportation and Logistics
Logistics is a crucial, often overlooked factor. The location of the supplier relative to the site can affect transportation costs. Bulk orders may reduce per-unit shipping fees, but logistics planning is essential to ensure that transportation costs do not unexpectedly inflate the overall project budget.
Cost-Saving Tips
To optimize costs without compromising quality, consider these strategies
- Compare multiple suppliers to identify competitive pricing, ensuring they maintain quality standards.
- Opt for standard sizes whenever possible to avoid custom manufacturing costs.
- Engage in long-term partnerships with suppliers to benefit from negotiated pricing.
- Evaluate the total cost of ownership, factoring in maintenance and lifespan, rather than focusing solely on initial purchase price.
Trust and Authority in Supplier Selection
Selecting a reputable supplier is crucial. Lean towards those who demonstrate a robust track record in providing high-quality galvanized grating and exhibit transparency in their pricing. Customer reviews, industry certifications, and the ability to meet project timelines are indicators of a supplier’s reliability. Furthermore, engage with experts to assess supplier offerings, ensuring that they align with project-specific requirements.
In Summary
Understanding the myriad factors affecting the cost of galvanized grating allows for informed decision-making that balances financial constraints with quality demands. By assessing material types, finishes, and supplier reliability, project managers can ensure that they choose the best products for both immediate and long-term needs. Ultimately, awareness and strategic planning are key to leveraging galvanized grating’s benefits while maintaining budgetary control.